Alle Jahre wieder sollte man bei 2 Zylinder-Motoren die Synchronisierung der Vergaser bzw. Drosselklappen vornehmen bzw. kontrollieren. Jedes Mal in die Werkstatt fahren? Der ambitionierte Schrauber macht das selbst. Nur wie?
Bekanntestes System sind zwei Messuhren. Das hat aber den Nachteil, dass selbige rein mechanisch sind und Ungleichheit vorgegeben ist. Hier behilft man sich durch über Kreuz tauschen zur Kontrolle. Ist immer irgendwie fummlig und die Messuhren kosten auch ganz schön Teuro.
Also etwas günstiger bitte. Eine Schlauchwaage ist auch eine Möglichkeit. Wenn der Schlauch lang genug ist und mit einer nicht zu dünnen Flüssigkeit gefüllt ist, kann man auch hiermit eine Synchronisation herbeiführen. Hier gibt es aber noch mehr ABER.
Ist durch einen Fehler im Unterdrucksystem eine Seite deutlich stärker, zieht es ruckzuck die Flüssigkeit in Richtung Motor rein. Nicht eben das, was man sich wünscht. Weiterhin darf der Schlauch nicht zu dünnwandig sein, damit er sich bei anliegendem Unterdruck nicht zusammenzieht. Und auch die Schlauchlänge spielt hierbei schon eine Rolle. Also optimal ist das auch nicht gerade. Dafür aber sehr preiswert.
Da mir beide Varianten nicht so gut gefallen, und in professionellen Motorrad-Werkstätten digitale Messgeräte zum Einsatz kommen (jedenfalls in der mir bekannten), habe ich mir mal so meine Gedanken darüber gemacht. Nachfolgend das Ergebnis der Überlegungen.
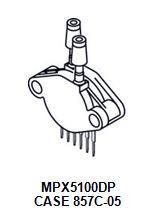
Grundsätzlich sind elektronische Sensoren auf keine mechanischen Komponenten angewiesen und unterliegen damit keiner Streuung wie beispielsweise eine Messuhr. Weiterhin kann eine rein digitale Verarbeitung der Messwerte kaum gestört werden. Und letztlich kann man Elektronik schön klein bauen.
Kern der Überlegung war, wie setze ich UNTERdruck in elektrische Signale um. Für diese Aufgabe gibt es recht preiswerte Drucksensoren. Die meisten dieser Art arbeiten jedoch von Null ausgehend positiv, also mit Überdruck und nicht mit Unterdruck. Ich habe aber einen Sensor gefunden, der über beide Messmöglichkeiten verfügt.
Jedem Zylinder wird nun ein solcher Sensor zugeordnet. Diese Sensoren sind vom Hersteller mittels Laser geeicht. Die Abweichung untereinander ist so gering, dass die gewünschte Messgenauigkeit für die Sychronisation weit übertroffen wird (Faktor 10).
Der Unterdruckbereich des Motors reicht bis maximal 1 Bar und entspricht damit optimal dem Sensor. Der normale Arbeitsbereich des Sensors geht bis 1 Bar. Bei vollem Druck ist die Ausgangsspannung des Sensors 4,7 Volt und lässt sich damit bestens weiter verarbeiten. Der Fehlerbereich liegt im Temperaturbereich von Null bis 85 C bei 2,5% maximal.
Rechnet man nun die Anzeige herunter auf zehn Stellen je Sensor, bekommt man als normale Auflösung 10% des Maximalwertes. Der Fehlerwert liegt deutlich darunter und spielt somit keine entscheidende Rolle und kann vernachlässigt werden. Auch bei zwanzig Stellen ist der theoretische Fehler ohne Betrachtung der Parallelität mit 5% deutlich über der Bauteiltoleranz.
Die Responsezeit des Sensors liegt bei 1 ms. Das bedeutet, dass ein Werteanstieg des Drucks von 10% auf 90% in 1ms am Ausgang erscheint. Das würde eine theoretische messbare Drehzahl von ca. 60.000 U/min ergeben. Also reichlich Reserve. Die Aufwärmzeit des Sensors liegt bei 20 ms, kann also ebenfalls vernachlässigt werden.
Es kommt als weiterer begünstigender Faktor hinzu, dass das System dual aufgebaut ist. Wenn durch Temperatureinfluss oder andere externe Einflüsse der Fehler in einem Sensor steigt, tut er es in selbem Maße auch im anderen Sensor. Die beiden Sensoren sind eine zusammengefügte Baueinheit. Da der eine Sensor in der Auswertung die Anzeige nach negativ und der andere die Anzeige nach positiv steuert, kompensiert sich hier der Fehler weitgehend von selbst.
Alles weitere ist nun nur noch ein wenig Elektronik Die Spannungen zu einer getrimmten Analoganzeige geführt. Diese beiden Pegelbalken liegen optisch nebeneinander. So kann man unabhängig vom Kurbelwellenversatz den absoluten Pegel je Ansaugtrakt sehen. Undichtigkeiten im Unterdrucksystem kann man hier gut erkennen.
Das Schöne an dieser Technik ist, sie kann fest im Motorrad eingebaut werden. So hat man jederzeit eine Kontrollmöglichkeit und/oder Einstellmöglichkeit. Preislich liegt diese Synchronisierhilfe bei ca. 70 Euro für Material. Das ist in etwa die Hälfte einer Messuhranlage. Nur mit dem Vorteil der höheren Genauigkeit.
In Kürze gibt es auch Bilder oder ein Video zur Funktion. ;-)
erster Versuch
Die ersten Tests zeigten die prinzipielle Richtigkeit der eingangs aufgezählten Eigenschaften. Allerdings sind die Berechnungen der Werte durch einen Controller für meinen Geschmack zu träge. Ich habe daher auf eine Mittelstellungsauswertung verzichtet und statt dessen eine Konstruktion gewählt, die weit sinniger ist. Beide Anzeigeskalen liegen nun direkt nebeneinander und man sofort erkennen, ob es eine Abweichung gibt. Wichtiger als der genaue Unterdruckwert ist ja genau die Abweichung untereinander.
Ganz nebenbei lässt sich damit auch ein Messgerät mit vier Kanälen aufbauen. Damit wären also auch die Vierzylindermotoren "versorgt".
Platinenlayout
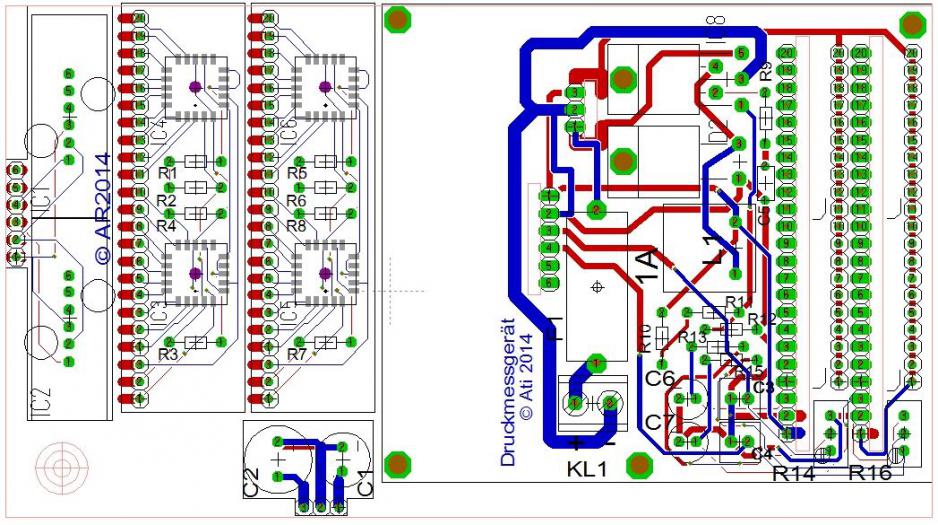
derzeit nur eine Neuigkeit. Platinenlayout ist fertig und erste Prototypen der Platinen sind geordert.
Platinen im Detail
Mein Prototyp ist fertig und eingebaut. Damit steht einer steten Kontrolle des Unterdrucks nichts mehr im Wege